The simple basics of electrical breakdown prevention
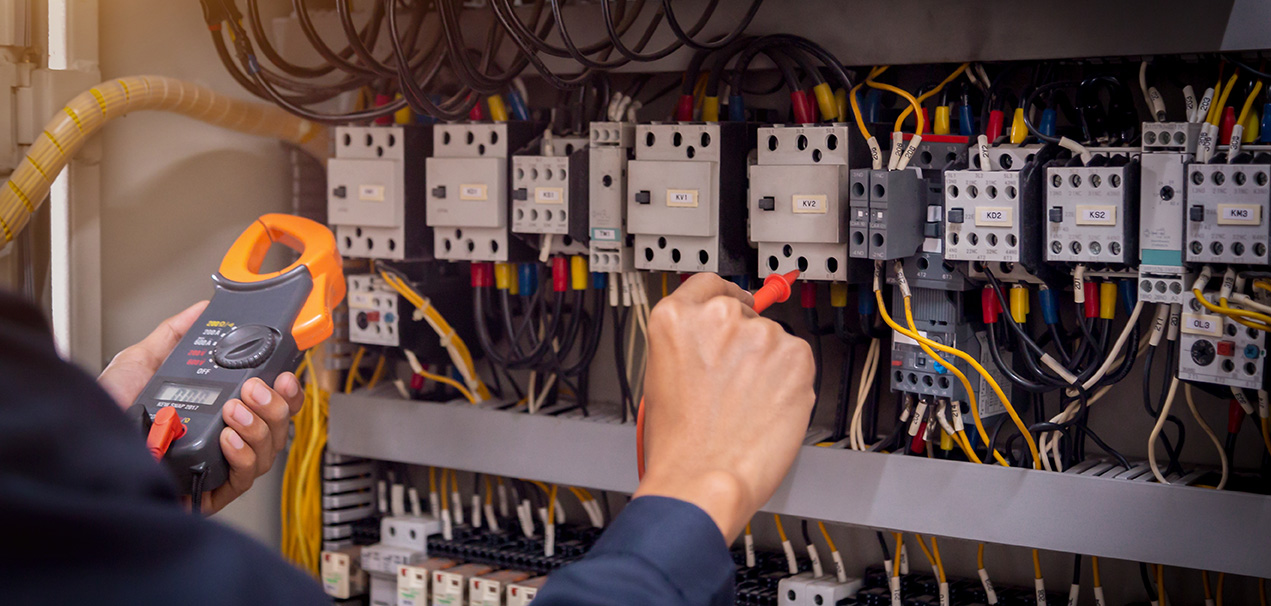
From its discovery early on as well as the many advancements throughout history, electricity and electrical power have revolutionized our world and how we exist in it. Lightbulbs to motors, heater elements to cellphones and computers, nearly every aspect of our lives involve or have been improved in some way by electrical devices. Much in the same way that electricity has revolutionized our lives, it came with great risk and changed the way we look at risk control. With light came heat, and with switches came arcs and sparks. The same wires that distribute the power could also break down and fail, resulting in fires and devastating loss to the equipment. Not only can the physical loss associated with electrical damage be significant, but the interruption to the business and the associated lost time connected to electrical equipment breakdown can be much more devastating. Take, for example, a loss of the main switchgear in an electrical room. It may be reasonable to assume the overall damage will be small and limited to that switch; however, the loss of that equipment would have far more reaching effects. Losing the switchgear could put that entire business into darkness for the duration of its replacement and if a replacement gear is not readily available that downtime could be extensive. Fortunately, there are a few simple, inexpensive measures businesses can take today to help improve the likelihood of preventing loss.
Electrical overview
Before reviewing the effects of electrical equipment breakdown, it is best to understand electricity and equipment in general. In simple terms, electricity is the flow of an electrical charge in a circuit. When a power source, whether a battery or generator, is connected to a circuit it creates that flow of electricity. That flow in a circuit is called the current, and another way to think of current is like the flow of water through a pipe. Much like the water’s flow is measured in gallons per minute, the current in a circuit is measured in amps. Keeping with the water analogy, like the pressure within a pipe, the "pressure" in the circuit is called the voltage and is measured in volts.
The typical equipment encountered in electrical systems first includes the switchgear, which act as the on/off switch for the circuit. Often an occupancy will have a main switch serving the entire facility and then additional smaller panels to control various sections of the building(s), equipment or business operations. When the switchgear is merely controlling whether the flow of electricity is on or off, circuit breakers and/or fuses are incorporated to protect against excessive current or too much flowing electricity. The circuit breakers and fuses are designed to detect excessive current and to respond and interrupt all flow to that circuit preventing damage to downstream equipment. This is critical in a situation where a circuit is overloaded with too many pieces drawing current or if there was a short circuit somewhere in the facility where the electricity essentially is leaking out of the circuit resulting in an excessive flow. Another important component of a facility’s electrical system are transformers. Recall that electricity has an associated voltage, or pressure, with which it travels to the facility. Should this voltage be too high for the building and equipment to handle, a transformer is supplied to “transform” that voltage to whatever the facility requires. Similarly, should the voltage be too low, the transformer can work the opposite way to increase the voltage as well. Finally, the last component in any circuit is the point of use equipment themselves. For instance, the lighting, the computers, any motors, etc. Each one of these components come together to make up the individual circuits or electrical systems.
Electrical hazards
Similar to fluid moving through a pipe, flowing electricity will create resistance or heat. Some factors that will affect or increase this heat include:
- The amount of electricity flowing through the circuit where the more flow results in more heat;
- The size or thickness of any wires connecting the equipment; or
- The material comprising the wires or equipment.
In addition, heat is created at any connection whether it be connections in the wires, connections at switches, or connections within the equipment itself. If any of these connections are loose or corroded it will intensify the heat generated. The production of all this heat can mean disaster for a facility. The heat in wires could break down insulation, creating bare spots and potentially an ignition source. If the bare wire does not ignite a fire, the heat generated within the wire or at the connections could easily ignite nearby combustible materials. Bare wires may also lead to a short circuit if other conductors are nearby.
In addition to the ignition source created by excessive heating, electrical components can also ignite fires by creating arcs or sparks. An arc occurs when a gap appears between two wires or other conductors and the electricity essentially jumps from one conductor across the space and then to the second conductor. The result is a high energy, high temperature, bright discharge between the two conductors that can ignite combustibles. A spark is a small high temperature particle that is discharged by an arc. These molten particles can move freely and ignite combustibles not in the immediate area of the arc. Again, loose connections, broken insulation or other damage to conductors and equipment can cause these arcs and sparks.
The final electrical hazard this article will cover is the arc flash. When an arc is large enough and is supplied with enough energy it can result in an uncontrolled and rapidly growing arc. This uncontrolled phenomenon is called the arc flash, which can produce an explosion with deafening noises, supersonic forces, superheated or molten shrapnel, temperatures in excess of the sun’s surface and an intense radiation capable of vaporizing nearby materials. Such a violent explosion would create significant destruction of the electrical equipment involved, any adjacent equipment and could easily lead to fire including combustibles not vaporized during the flash.
Prevention
Fortunately, there are a few simple actions that a business owner can take to reduce the potential for electrical equipment breakdown and fire potentials. Remember the following: Cool, Clean, Dry and Tight. These four words will help prevent or reduce many of the electrical equipment breakdown incidents.
- Cool – By ensuring your electrical equipment is both running cool and operating in a cool environment, the damage caused by heat is greatly reduced. This can also extend to the use of thermography or infrared scans of the electrical equipment. By finding hot spots in the electrical system, the tech can find issues before they become problems.
- Clean – By keeping electrical equipment clean, accelerated damage and breakdown can be avoided. Motors that operate in dirty environments build deposits. These deposits not only prevent the motor from cooling itself but create additional friction and wear and tear. The same goes for electrical panels, breakers, switches, etc. Keeping the equipment in a clean environment can extend life.
- Dry – Most everyone can agree that moisture and electronics do not mix. But why? What is it exactly that is feared? As discussed earlier, shorts and arcs are created by stray electricity finding unintended paths. Water can be a major culprit in creating these alternate paths for the electricity to stray. However, even if the equipment isn't wet necessarily, wet environments will speed corrosion to all exposed metal. Corrosion on equipment will interfere not only with the equipment's operation but will also create more heat, more wear and tear and shorten equipment lifespan.
- Tight – Loose connections build heat and eventually, if left alone long enough, can create arcing and sparking. Thermography is a great tool to catch these connections before becoming larger problems.
These four simple considerations, in conjunction with a comprehensive inspection testing and maintenance program, will combine to reduce the occurrences of many potential equipment breakdown headaches. Headaches that will include not only the loss of the equipment itself, but the lengthy and costly downtime to a facility caused by the loss of production.
Additional resource:
- Contact us for a copy of the Hazard Guide on Electrical Preventive Maintenance and/or Risk Indicators for Electrical Switchgear
- Electrical breakdown