The FM equipment factors
An equipment breakdown can significantly disrupt operations for any business. Keeping a facility operational depends on how well equipment is designed, installed, operated, maintained, and protected. To minimize equipment loss or business downtime, a comprehensive understanding of equipment risk is essential.
FM defines seven major equipment factors that drive the frequency and severity of breakdown to equipment. Each of these observable conditions can be assessed and rated as “satisfactory” or “unsatisfactory.” Based on FM’s loss history and data analytics, the more factors rated unsatisfactory, the higher the chances of equipment failure and increased risk exposure.
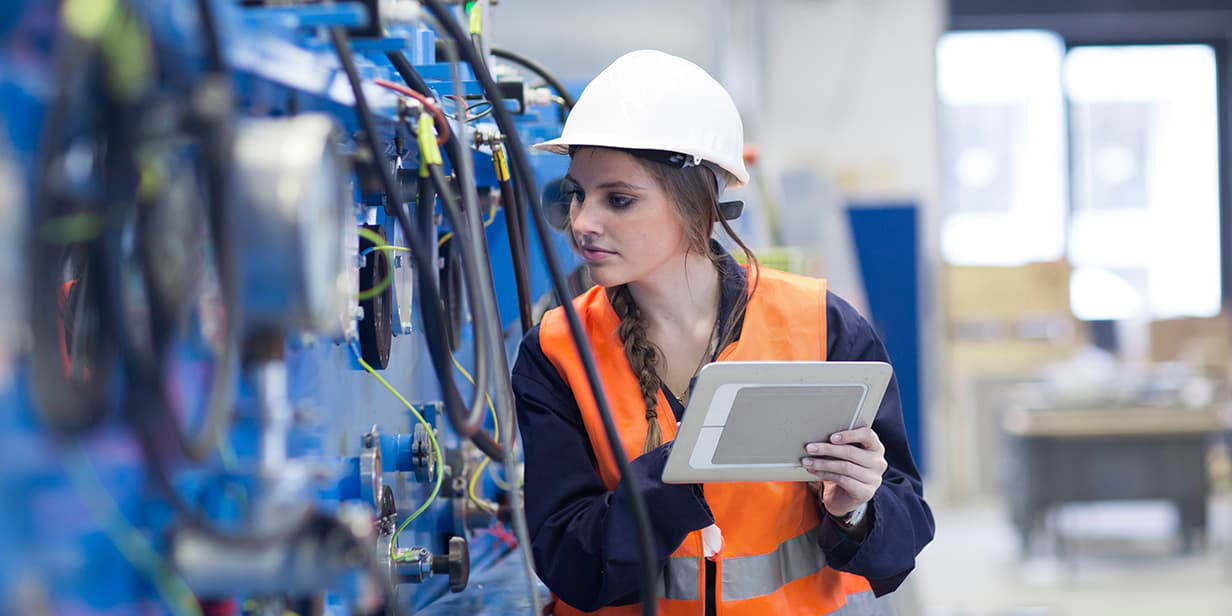
Frequency risk indicators
Unsatisfactory ratings within the factors below increases the likelihood of equipment breakdown.
- Maintenance - Adequacy of inspection, testing, and maintenance programs to verify asset integrity, reliability, and fitness for service. A facility should have a comprehensive formal preventive maintenance program based on OEM guidelines and industry standards.
- Environment - External operating environment and physical conditions/surroundings in which the equipment is operating, considering the suitability of the equipment for the service environment. Conditions such as excessive dust, dirt, moisture, and heat can stress equipment and reduce its normal expected operating life.
- Operators - Effectiveness/adequacy of training, qualification, and retraining programs to standard and emergency operating procedures to ensure operation of equipment and processes within design limits during normal and upset conditions. Having a formal operator training program in place that is regularly audited will help prevent losses caused by operator error.
- Operating conditions - Actual operating conditions vs. design conditions, including overloading, cyclic use, and/or process upsets outside of design limits. Equipment should be operated and maintained within OEM specifications and should be taken out of service when monitoring parameters are exceeded.
- History - Operating history including failures/breakdowns/process upsets resulting in deterioration and service aging, impacting remaining life. Equipment with a repair history or needing excessive maintenance is more prone to loss.
Severity risk indicators
Unsatisfactory ratings in the factors below increases the severity of equipment failure.
- Contingency planning - Preparedness in advance to respond to and recover from an unplanned failure of equipment resulting in a significant interruption to key site processes, including the viability of sparing where provided. Facilities should have a formal written contingency plan for key equipment that could include housing critical spares, having contracts with equipment rental companies, and arranging for alternative solutions.
- Safety devices - Protection devices (safety or control) are adequately designed, installed, maintained, and functional to protect equipment during normal and upset operating conditions. Any control equipment or safety devices should be adequately installed and properly tested to ensure functional reliability.
How to get started
FM’s 10-year loss history study revealed that the frequency and severity of loss increase with the number of unsatisfactory equipment factor ratings. Performing a comprehensive risk evaluation of equipment based on the seven factors is the first step and will provide a starting point for identifying which equipment may be at risk. Prioritize improvements for any equipment with unsatisfactory ratings, focusing on the factors identified as the three main loss drivers:
- Maintenance
- Operators
- Safety Devices
Ensuring these factors rate as satisfactory will help reduce the frequency of loss.
Additional resource:
- Data Sheets - The FM Property Loss Prevention Data Sheets provide various guidelines for many pieces of equipment such as transformers, switchgear, and electrical panels.