Pressure systems breakdown
In the equipment breakdown space, “pressure systems” refers to commercial boilers and pressure vessels. Today, pressure vessels are used in a wide range of applications including steam and hot water boilers, which can be found in almost any occupancy. The steam or heat produced by these units is used to power machines and heat buildings, or as a means of processing materials. While pressure vessels are essential for many industries, this type of equipment can be dangerous. If they are not properly maintained, they can lead to significant loss in both property and life.
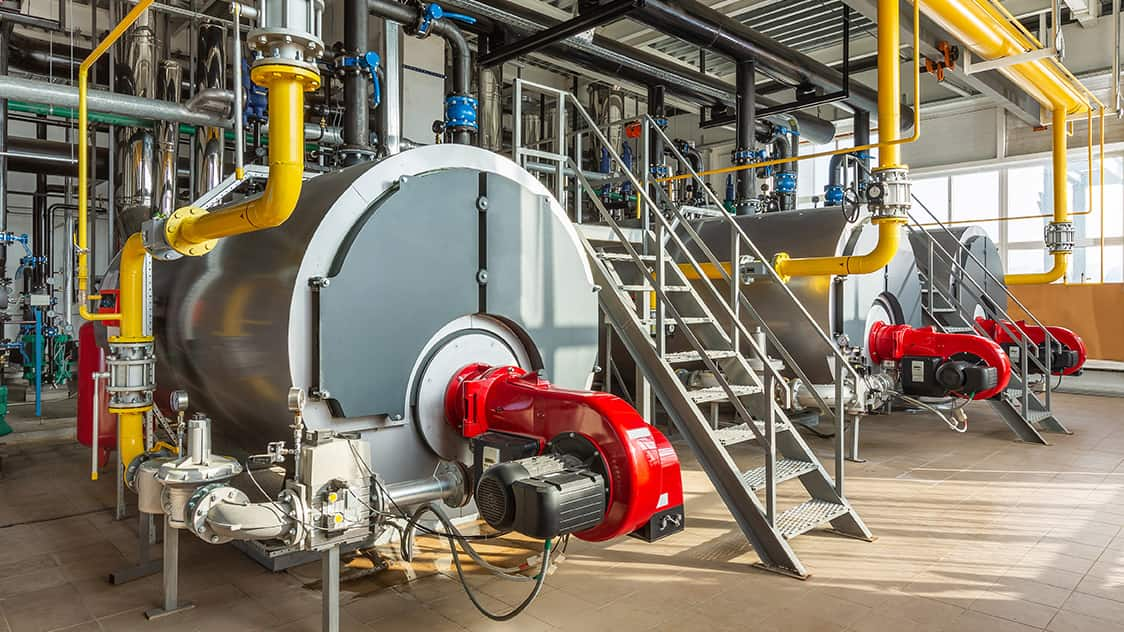
While a boiler is considered a pressure vessel, it is specifically a closed vessel in which water or other fluid is heated to produce hot water or steam. The heat is produced by burning fuel such as natural gas, oil, coal or biomass. Pressure vessels are simply containers that hold pressurized liquids, vapors or gases. Common examples of pressure vessels include compressed air receivers, hot water storage tanks and process storage vessels.
Why are pressure systems dangerous? A pressurized vessel stores large amounts of energy that, if not controlled, can lead to significant losses including costly repairs, business interruption and even catastrophic accidents. Boilers can be particularly vulnerable to destructive failure if it results in a steam or combustion explosion – an event that has the potential to cause widespread property damage, injuries and fatalities.
Pressure systems hazards
- Low water/dry fire - A boiler needs sufficient water not only to produce steam or hot water but to also keep metal parts cool, such as tubes, shell and cast-iron sections. Typical furnace temperatures can be as high as 1,800 °F / 3,272 °C. At that temperature, metal strength quickly weakens and ultimately fails without the cooling effects of water. Failure to maintain proper boiler water levels will create a low water condition that can cause cracking, bulging and, in the most extreme cases, steam explosion and catastrophic failure of the boiler. Critical safety devices such as low-water trip switches protect the boiler from operating in a low water condition, but require proper installation as well as regular maintenance and testing.
- Poor water treatment - Corrosion of the pressure retaining metal parts can lead to wearing and thinning of material and structural failure. In addition, scale buildup on boiler surfaces acts as an insulating layer that reduces heat transfer efficiency and overheating of critical parts. To combat this, boiler water is chemically treated to reduce the level of solids and oxygen. Failure to maintain appropriate water chemistry, along with conducting regular surface and bottom blowdown of the boiler, will lead to corrosion and scale levels that adversely affect vessel integrity.
- Furnace explosion - One of the most dangerous situations of boiler operation is a fuel explosion in its furnace. Boilers are predominantly fuel-fired equipment. When unburned fuel from the burner accumulates in the furnace and ignites, it can do so in a very rapid or explosive manner that can cause severe damage to the boiler and its surroundings. The most common causes are fuel-rich burner mixtures (insufficient air), poor atomization of oil causing incomplete combustion and improper furnace purge following a burner trip. Proper maintenance and operation of the boiler is essential to preventing furnace explosions from occurring.
- Lack of maintenance and testing - As with any important equipment, boilers and pressure vessels need to be properly maintained, tested and operated to prevent adverse conditions from developing and causing costly damage. The leading contributors of pressure equipment loss include operator error and lack of maintenance and testing. Implementation of a formal preventive maintenance schedule, including regular testing of all critical safety devices, is the most important preventive measure to help avoid boiler losses. This, in addition to ensuring there are adequately trained operators or personnel, is the cornerstone of safe boiler operation.
Loss prevention
Keep the boiler room clean and clear of any unnecessary items.
- Ensure all personnel who operate or maintain the boiler room are properly trained.
- Develop a formal boiler and pressure vessel maintenance program that includes:,
- Maintenance checklist and schedule
- Operator log sheets
- Maintenance and testing records
- Repair documentation - Conduct regular tours of the boiler room to observe operating conditions and look for signs of abnormal conditions.
- Contact a qualified service technician to service the boiler at least once per year.
- Implement a documented boiler water treatment program with a reputable chemical treatment contractor.
- Verify that the water treatment system is operating properly.
- Perform regular surface and bottom blowdowns.
- Annually inspect and test boiler fuel train components.
- Maintain current operating certificates by ensuring that the jurisdictional required boiler and pressure vessel inspections are conducted by an authorized inspector at its designated frequency.
Proper care and operation of critical pressure equipment will minimize damage, repairs, interruption of business – and injury to personnel. The majority of boiler and pressure vessel losses could be prevented or reduced with proper operator training and an Asset Integrity program that includes a documented Inspection Testing and Maintenance program.
Additional resources: