Hot work hazards
Strategies to safeguard facilities
Businesses often rely on hot work for new installations and repairs within their facilities. Hot work is considered any temporary operation involving open flames or producing heat and/or sparks and includes brazing, cutting, soldering or welding. These activities can introduce an ignition source if not properly managed, which could lead to catastrophic, yet preventable fire events. Among FM clients, hot work is the second leading cause of fires, following electrical issues. Consequently, it is imperative for businesses to accurately identify and manage hot work to mitigate their fire risk.
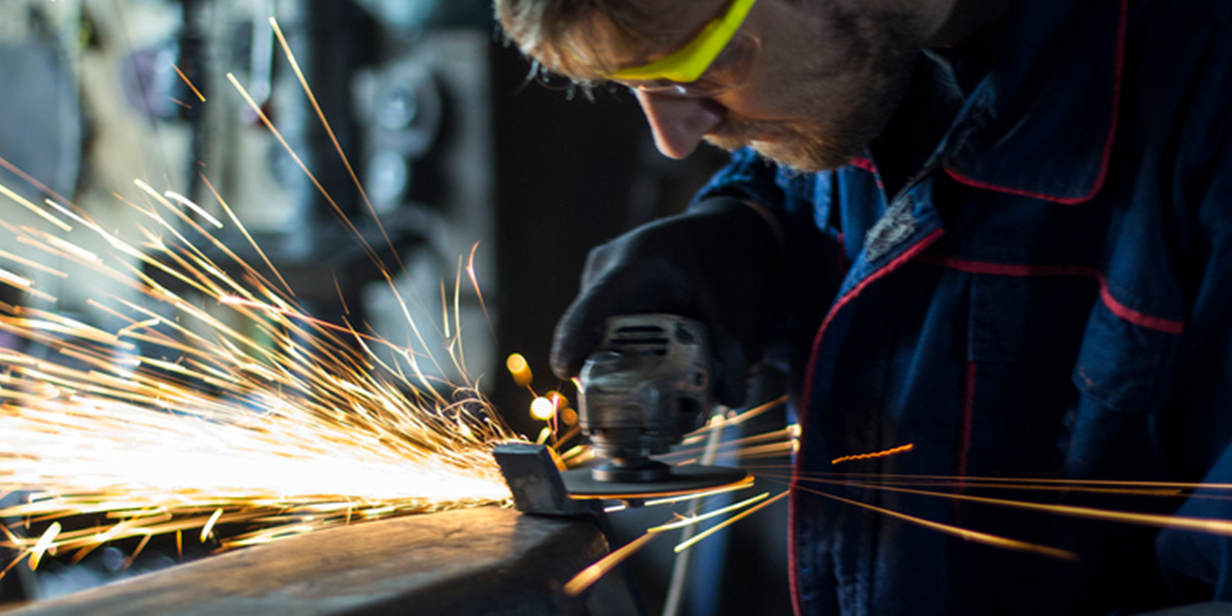
Managing hot work
Effective management of hot work is crucial for mitigating fire risk. Facilities can significantly reduce hot work fire risks by implementing various best practice measures.
Hot work permit system – The hot work permit system aims to document proper procedures before, during, and after hot work, including details of the personnel involved, the method used, and the precautions taken.
Contractor management – Effective contractor management is critical as FM’s client loss history indicates a heightened fire risk when outside contractors perform hot work. Contractors may not fully understand the fire hazards specific to a facility. In order to reduce fire risks, facilities may consider the following recommendations before work begins:
- Ensure contractors are utilizing the hot work permit system
- Provide contractor training including a brief overview of the facility with an emphasis on fire related hazards
Housekeeping – Good housekeeping serves as a crucial safeguard against hot work fires, significantly reducing their magnitude or preventing them altogether.
- Cleaning debris – Ensure floors and work areas are clear of combustibles and refuse.
- Ignitable liquid and residues – Promptly clean up spills and equipment to prevent excessive build-up of oily residues.
- Proper storage – Store combustible materials in designated areas, such as racks, and away from work zones.
Equipment to manage hot work – Use fire resistant welding pads and blankets to shield combustible materials from hot work sparks and weld curtains to enclose hot work areas.
Fire watch – Fire resulting from hot work can ignite up to 3 or more hours after work is complete. Designate personnel to serve as a fire watch to monitor areas during and after hot work. Ensure the fire watch is trained to respond to fires. FM recommends a 1-hour active fire watch, followed by a 3-hour monitoring period.
Designate a hot work area – Designate an area specifically constructed, protected and arranged to accommodate safe hot work. These areas do not require any permit system but appropriate firesafe conditions should be maintained within them.
Annual training – Provide all site personnel with annual training on hot work, including risk reduction and an overview of the hot work permit system.
Alternative methods
To reduce or eliminate the risk of fire, consider using “cold” methods, where appropriate, or relocating the work to a hot work designated area.
Hot work alternatives
- Mechanical connections vs. welded
- Hydraulic shearing
- Threading pipe vs. sweat-soldered pipe
- Self-tapping screws vs. tack welding or brazing
Less hazardous hot work*
- Heliarc welding vs. electric arc-stick welding
- Electric heat gun vs. open-flame torch
- Electric soldering iron vs. torch soldering
*Hot work management is still required
Prioritizing hot work loss prevention management reduces fire risk and enhances operational resilience. Through a variety of safety measures, facilities can protect their property and valuable equipment before, during and after hot work activities. Access FM resources to better understand hot work risks and loss prevention methods.
Additional resources:
- FM Hot Work Permit System
- Data Sheets – Property Loss Prevention Data Sheet 10-3, Hot Work Management
- Understanding the Hazard – Hot Work – available in the FM Resource Catalog
- FM Approvals Guide – Identify FM Approved Hot Work management equipment